
WELDING
*Welding is the process of joining two plastic or metal parts by melting them, with or without using a further molten material.
*Welding is a process of joining two metal pieces by the application of heat. Welding is the least expensive process and widely used now a days in fabrication.
*Welding joints different metals with the help of a number of processes in which heat is supplied either electrically or by mean of a gas torch.
*Different welding processes are used in the manufacturing of Auto mobiles bodies, structural work, tanks, and general machine repair work.
Classification of Welding Process
*The number of different welding processes has grown in recent years. These processes differ greatly in the manner in which heat and pressure are applied, and in the type of equipment used. There are currently over 50 different types of welding processes.
1. Oxy-fuel welding – also known as oxyacetylene welding or oxy welding, uses fuel gases and oxygen to weld and cut metals.
2. Shielded metal arc welding (SMAW) – also known as "stick welding or electric welding", uses an electrode that has flux around it to protect the weld puddle. The electrode holder holds the electrode as it slowly melts away. Slag protects the weld puddle from atmospheric contamination.
3. Gas tungsten arc welding (GTAW) – also known as TIG (tungsten, inert gas), uses a non-consumable tungsten electrode to produce the weld. The weld area is protected from atmospheric contamination by an inert shielding gas such as argon or helium.
4. Gas metal arc welding (GMAW) – commonly termed MIG (metal, inert gas), uses a wire feeding gun that feeds wire at an adjustable speed and flows an argon-based shielding gas or a mix of argon and carbon dioxide (CO2) over the weld puddle to protect it from atmospheric contamination.
5. Flux-cored arc welding (FCAW) – almost identical to MIG welding except it uses a special tubular wire filled with flux; it can be used with or without shielding gas, depending on the filler.
6. Submerged arc welding (SAW) – uses an automatically fed consumable electrode and a blanket of granular fusible flux. The molten weld and the arc zone are protected from atmospheric contamination by being "submerged" under the flux blanket.
7. Electroslag welding (ESW) – a highly productive, single pass welding process for thicker materials between 1 inch (25 mm) and 12 inches (300 mm) in a vertical or close to vertical position.
8.Electric resistance welding (ERW) – a welding process that produces coalescence of laying surfaces where heat to form the weld is generated by the electrical resistance of the material. In general, an efficient method, but limited to relatively thin material.

Welded Joints
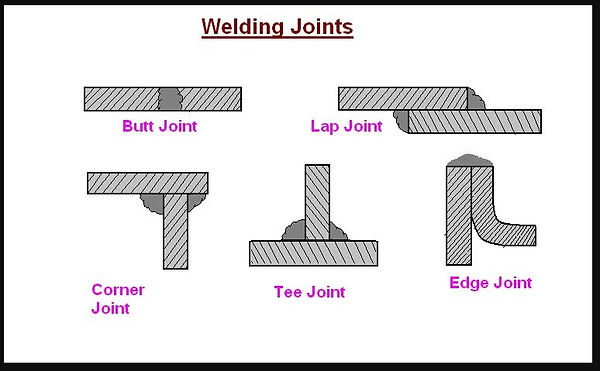

